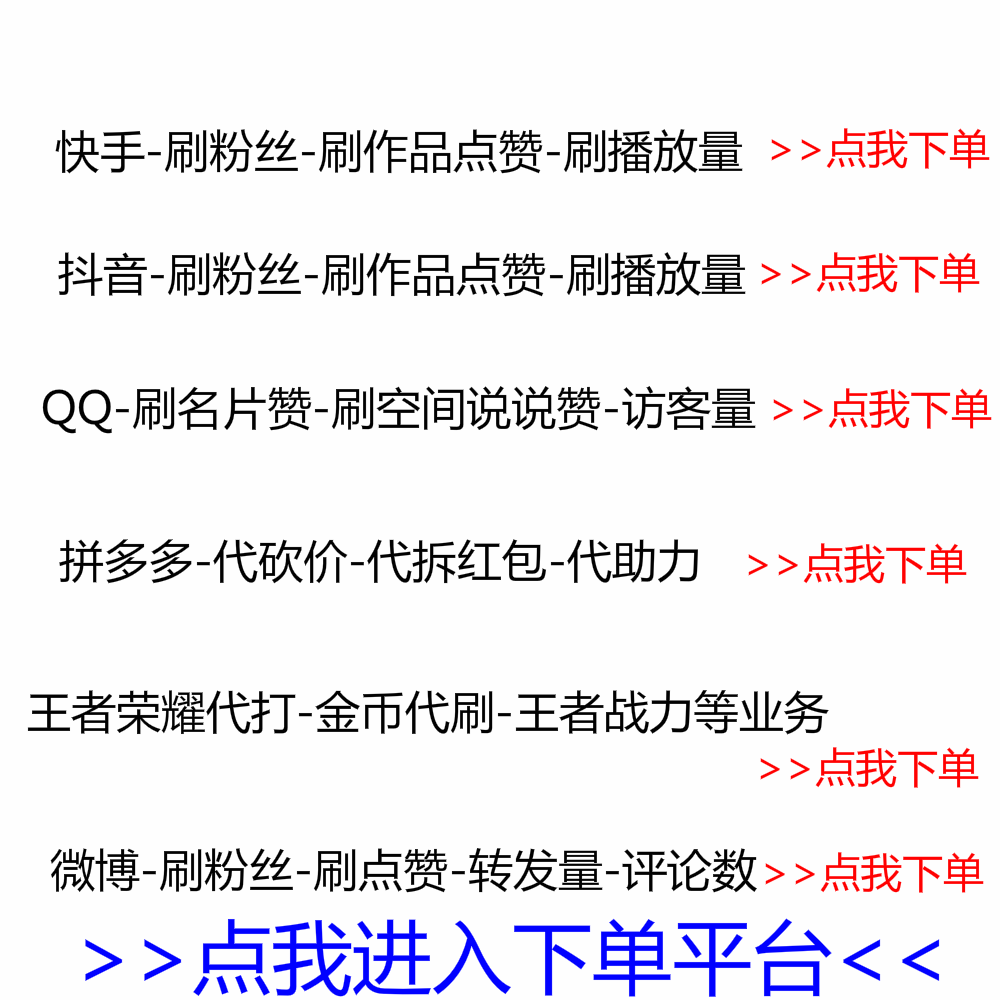
药品生产管理流程
管理是各种组织中最普遍和最重要的一种人类活动。以下是小编收集的药品生产管理流程,欢迎查看!
批量生产记录
生产记录是对一批药品生产过程中各工序全过程(包括中间控制)的完整记录,应具有质量可追溯性。
一、批处理
批的概念:一定数量的在规定限度内具有相同性质和质量的药品,在同一连续生产周期内生产的药品为一批。
1. 大、小容量注射剂一般是同一个配液罐一次性制备的一批均质产品。
2.粉针剂一般是用同一批原料药在同一连续生产周期中生产的一批均质产品。
3.冻干粉针剂是同一批次药液,在同一生产周期内使用同一冻干设备生产的一批均质产品。
4.在成型或分装前使用同一混合设备一次性混合固体和半固体制剂生产的一批均质产品。
对于固体制剂,若以多次混合后的产品作为批号,必须进行验证,证明产品质量的均匀性,在规定限度内生产的产品为批次。一般采用多维运动混合机等最终混合设备混合一批。
5.液体制剂(包括膏剂、浸膏、浸膏等)是在灌封(包装)前将药液最终混合生产的一批均质产品。
6.原料药的连续生产,在一定的时间间隔内生产的一批在规定限度内的均质产品。
对于批量生产的 API,通过最终混合数学确定的产品获得的一批在规定限度内的均质产品。混合前的产品必须采用相同的工艺生产,符合质量标准,并有可追溯的记录。
7.生物制品的生产,按照《中国生物制品条例》中《生物制品批号》的规定进行批号、批号。
需要注意的是,由两台或多台压片机(胶囊充填机)压制成的片剂,必须检查片重差异(充填量差异),并确认在同一合格范围内,符合其质量要求后要求仅作为一个组。
二、批号
批号的定义:一组数字或字母数字,用于识别“批”,用于跟踪和审查该批的制造历史。必须为生产中的每个批次准备一个生产批号。
如何准备批号
1. 普通批号:年月流水号,如批号011201,即2001年12月的第一批。或取年月日流水号,如批号0112012,即批号第二制剂2001年12月1日生产的批号。或用数字和字母,用英文字母表示生产车间或剂型。
2. 再加工批号:再加工后的批号保持不变,但在原批号后面加了一个代号以示区别。代号由企业确定,如年月日序号(代号)。
3.混批号:年-月-流水号(代码),如0112/03-05,表示混批号为2001年12月第三批至第五批,共3批,代码由公司确定并由车间填写混批登记表。
需要注意的是,药品的分装仅限于一个合箱内分两批,合箱外应标明所有批号,并建立合箱记录。
三、批量生产记录
1.批量生产记录的定义:一批待包装产品或成品的所有生产记录。批生产记录应提供该批的生产历史和与质量有关的情况。
2.批生产记录的内容:产品名称、生产批号、生产日期、操作人员、审核员签名、相关操作和设备、相关生产阶段的产品数量、物料平衡计算、生产过程控制记录和记录特殊问题。
3.批量生产记录填写
岗位作业记录由岗位操作人员填写,由岗位领导、工匠审核签字;批量生产记录由车间技术人员收集,车间技术负责人或专职车间工程师审核签字,跨车间产品由各车间分别填写,由工厂填写。生产技术部指定专人审核并签署总结。成品放行前,工厂质量管理部门审核批生产记录并签字,决定产品的最终放行。
GMP规定批生产记录要写清楚,内容真实,资料齐全,并由操作人员和审核人员签字。记录应当保持整洁,不得随意撕毁、涂改。进行更改时不合格品控制程序英文,对更改进行签名并使原始数据仍可识别。
批生产记录填写要求:
① 内容真实,记录及时;
②字迹清晰,不宜用铅笔填写;
③不得随意撕毁或涂改。需要更改时,用一条或两条横线标出更改的地方,并在签名和日期旁边改写正确的数据,使原来的数据仍能辨认;
④根据内容完整填写表格,资料齐全。除备注栏外,不允许有空格。如无内容填写,用“-”表示;
⑤ 如内容与上一项相同,应重复填写,不能用“……”或“同上”或“同左”表示;
⑥产品名称应写全称并按标准名称填写,不得缩写;与其他岗位、团队或车间相关的操作记录应保持一致、连贯;
⑦填写的日期横写,不得缩写;
⑧ 签字时要写全名,不能缩写;
⑨ 数据的四舍五入原则应以相同的舍入机会进行,即“4”轮、“6”轮、“5”双。
4.批生产记录审核注意事项:
必须根据每批后期操作记录进行系列审核;
记录内容必须符合生产工艺规程和后期操作规程;
上下工序、成品记录中的数量、质量、批号、容器号必须一致、正确;
生产中不符合要求的灌装方式,必须由灌装人员改正并签字;
发现异常情况,必须查明原因,作出合理解释,并作详细记录。负责人和审稿人必须签字。
5.批量记录保存:
批量生产记录应按产品类型分批归档保存,直至产品保质期后一年。
生产过程技术管理
一、生产准备期间的技术管理
1.生产管理部根据企业的生产销售情况,安排生产计划,编制批量生产指令,下发给生产、材料、质量等相关部门。同时,将相应的批量生产记录下发到操作车间。
2.在生产车间,根据批量生产指导书、生产工艺规程和岗位标准操作规程,车间工艺技术人员会对每一道工序下达生产计划,每一道工序都会根据仓库配额从仓库中领取物料。计划。规格、批号、厂家、数量、检验报告等,填写拣货记录。
3.对于影响制剂或成品原料药质量的原辅材料,当货源或批号发生变化时,应进行小样试制,确认符合要求,然后填写小样试生产合格报告。生产。
4.生产作业开始前,操作人员必须检查工艺卫生、设备状况等,检查内容包括:
①检查生产现场的卫生情况是否符合该区域的卫生要求;
②变更批号品种规格前,必须有上批产品的“清关证明”复印件。未取得《清关证复印件》,不得生产不同规格或不同批号的其他品种或同一品种的产品;
③设备清洁完好,有“设备清洁状态标志”;
④ 计量器具与称量范围一致,清洁完好,有《计量检定证书》,在周检有效期内;
⑤ 正在维修或停用的设备应标明“不使用”状态标志。检修完毕后,应由设备操作人员进行验收,并应清洁、符合要求。只有设备完好才能使用;
⑥ 衡器、量具在使用前应进行检查和校准,对生产中使用的计量、检测仪器、仪表进行必要的调试;
⑦所用的各种材料和中间产品应按质量标准检查检验报告,中间产品应有质检员签字的交货单,认真鉴别。
⑧ 盛放物料的容器外必须有标签。标签上应标明产品名称、规格、批号、重量(皮重、毛重、净重)或数量、本批次容器个数及加工状态、工序名称、操作日期及班次、操作人员、审核人员、等等
二、生产过程中的技术管理
1.根据GMP规定,生产过程中物料的投料、称重、计算等操作必须有专人审核。操作人员和审核人员应在操作记录上签字,车间技术人员和质量人员均应予以答复。监督关键操作。麻醉药品、精神药品、有毒药品、放射性药品和贵重药品,要按照国家有关规定严格执行。使用后剩余的散装物料应及时封存,操作人员应在容器上注明开封日期和剩余数量。、用户、审稿人签收,专人办理退换货手续。原辅材料拆包再次使用时,应核对记录,并应检查外观和性能。如有异常或不稳定性质,应再次送检,合格后方可使用。
每批生产后的余料由操作人员及时退回库房,车间不得存放未使用的余料,中间站存放的中间产品除外。
2.生产工艺规程和标准操作规程
生产工艺规范:规定生产一定数量的成品所需的起始原料和包装材料的数量,以及工艺、加工指导、注意事项,包括一个或一组控制生产过程的文件。
标准操作程序:批准用于指示操作的通用文件或管理方法。
后期作业应按生产工艺规程规定的工艺条件和标准作业规程规定的作业方法进行。生产工艺规程和标准操作规程一经制定,不得随意更改。
企业生产技术部门和车间工艺技术人员必须检查生产工艺规程和标准操作规程的执行情况,即制定工艺验证制度,定期进行工艺验证,并详细记录,确保准确执行。工艺规程和操作规程。工艺验证内容由企业根据各岗位操作规程要求、各工艺参数执行情况、洁净区(室)温湿度、定期检查人数等要求进行核对。粉尘颗粒、微生物数量、质量抽检记录、工艺卫生和批量生产记录。
中药制剂车间一般生产过程控制要点有:(以片剂为例)
①提取物的比重、量、醇沉醇浓度等;
②中草药粉的粒度、水分、微生物数量、粉碎物料平衡收率等;
③制粒过程中的粘合剂配比、使用量、制粒温度、粒度、水分含量、含量均匀度等;
④压片的硬度、脆碎度、崩解时限或溶出度、片重差异、外观等;
⑤片剂包衣液情况、包衣片外观、崩解度、片增重等;
⑥内包装工艺的包装数量、外观、密封试验等;
⑦外包装工艺标签、使用说明书的使用、外包装数量、包装质量等。
3.不同产品品种、规格的生产作业,不得在同一作业意见下进行。同一品种、同一规格、不同批次的制剂生产、包装作业在同一操作间进行时,采取隔离或其他有效防止污染或混淆措施。
生产操作人员在操作过程中动作要平稳、轻快、少,不要做与生产无关的动作和不必要的谈话,更不要在生产作业现场大笑、打闹、大声唱歌。
4.生产过程中每个关键工序都要严格计算物料平衡,只有在规定的范围内才能流入下一道工序。超出范围的,按偏差处理程序进行分析调查,并经质量管理部门批准。
在生产过程中,如发现物料异常情况或可能存在的质量问题,操作人员无法自行决定,需要向相关人员和车间领导报告,并按偏差处理程序进行处理。最终,质量管理部门决定材料的使用权。质量管理部门要遵循“三个不放过”的原则,即不合格的原辅材料不投入生产,不合格的中间产品不流入下道工序,不合格的成品不离开工厂。
生产过程和中间产品必须由质量管理部门的质量控制人员严格监控,并在批记录的背面附上各种监控证明。
如果生产过程中出现问题,当设备需要调整或维护时,应停机运行,切不可开机,以免发生安全事故和对人员造成伤害。
5.设置管理
为便于养成良好的生产习惯,减少出错的可能性,车间应进行固定管理。
生产作业和设备应按工艺流程顺序合理安排,使物料生产同向流动,避免物料交叉流动,减少交叉污染的可能性,不遗漏任何生产工序.
手术室的放置管理是指严格规定手术室设备、各种材料、容器、手术台的放置。生产中使用的工具和工具,使用后应放回原位,不得丢弃或放置在设备内,以免发生生产事故。
中转站等其他房间也应按固定位置管理。例如,在卫浴间应明确各种清洁工具的存放位置,并严格执行定点管理制度。
6.状态标志管理
与设备相连的主要固定管道,包括工艺用水管道,应标明管道内物料的名称和流向。管道应安装整齐有序,或涂上不同颜色以示区别。如物料管道
– 黄色,蒸汽管
– 红色的饮用水管
– 蓝色,压缩空气管路
——白等,各企业可根据自身实际情况确定。物料的流动方向由喷涂颜色的方向表示。
每个生产操作间还应有状态标志,指示操作间当前的生产状态。生产时应注明所生产的品种、规格、批号、生产日期、操作人员等;未生产时,应注明清洗、待清洗等,清洗状态应标注清洗有效期、最后一批产品名称等;未使用的房间应留作使用标志。
设备状态为清洁、在用、待机、已修、待修等。使用时应注明产品品种、规格、批号、生产日期、操作人员等,并有固定状态标志设备应标明设备型号、设备负责人等。材料和使用容器还应有状态标志,其内容见以前的容器标签。
7.包装标签管理
对符合生产工艺规程要求的产品,整个生产过程在质量管理部、车间工艺技术员和质量员的监督下完成,检验合格的产品可以由生产管理部门进行管理。
该部门发布批量包装指令。对一些检验周期长、检验结果前需包装的制剂产品,允许先包装后作为入库产品处理,检验合格后方可入库。程序被处理。
包装中使用的标签和使用说明书必须由车间填写,并送至标签库领取配额,并由拣货员和寄件人签字。印有批号的标签、残留、不完整的标签或取消批号时的标签,或车间贴标过程中的剩余标签不得回收。主管签字。
车间应设立标签库,由专人负责标签的收集和发放,并按品种、规格分类,存放在标签库中。
锁存,登记备案,印有批号的标签,分批存放。产品包装完毕后,包装工序会派专人到车间领取,并按批次包装说明填写领取记录。
每批产品包装完成后,应及时填写包装记录,如实填写使用的包装材料数量。如果使用数量+剩余数量+破损数量之和不与收到的号码不符,应查明原因并记录。标签不得改变用途或更改以供后续使用。
8.中间站管理
车间生产的中间产品应存放在中间站,不得长期存放在操作间内。中间站的存放范围包括:中间产品、需再加工的产品、清洁的周转容器等,除上述以外的物品不得存放在中间站。材料不能回收!进入中转站的物品外包装必须清洁,无浮尘。
中间产品在中间站应有明显的状态标志,标明产品名称、批号、规格、数量,并按品种、批号整齐排列。不同品种、不同批号、不同规格的产品之间应有一定距离。应密封保存。其中“红卡”表示不合格,“黄卡”表示待检,“绿卡”表示合格,“白卡”表示待再处理,并堆放。
操作人员每天及时将物资存放在中间站,并填写中间站的入库记录。中间站管理员核对产品名称、规格、批号、重量(数量)、容器数量、工艺名称、加工状态等,无误后核对外包装。由供料者和中转站管理员签字,填写进场日期,并按规定堆放整齐。中间站管理员填写中间产品台账和中间站物料卡,中间站进入记录应附在批量生产记录中。
中间站存放的资料应与账户、卡片、资料一致。质量管理部主管、车间工艺技术员、质检员应定期检查中间站的物料状况。
中间站管理员要求对中间产品进行检验。此时,材料应标有待检状态标志。检验合格后方可加贴合格状态标志,或由质量管理部门颁发中间产品合格证书。
中间站管理员根据车间下达的工序生产指令,将合格的中间产品下发到下一道工序,并填写中间产品出库记录。共同签名,同时填写中间平台账号和KUKA。
中间站应锁定管理。管理人员离开时,应在离开前锁好房间。
9.不合格品管理
对经质量管理部门检验确认不合格的产品,检验部门出具不合格品检验报告。合格的产品加工程序及时办理。
不合格品一般按生产管理
该部门会同有关部门分析提出处理意见,报质量管理部门审核批准。
10.模具和筛网管理
车间设备人员应对生产使用的模具建立档案,存放在相应的模具室。模具使用前后,检查其平整度、备件是否齐全、有无破损、是否符合生产要求等,并填写模具使用及配送记录。损坏的模具应在合格后方可修复使用。不能继续使用的,应办理报废手续,根据实际情况申请购买。
使用筛网前,应检查其完整性,是否符合生产工艺要求。存储的每个屏幕都应标有其规格(网格)。在生产过程中,应经常检查筛网的使用情况。如有损坏,应追查原因,是否影响产品质量,经必要处理后方可继续生产。如果是质量问题,应上报车间领导和质量管理部门解决。
在生产过程中,一般采用不易与药物发生化学反应的不锈钢或尼龙网。
11.生产过程中产生的特殊材料的管理
①粉体管理
粉头是指在生产过程中产生的少量合格、可回收或未使用的材料。如胶囊填充完成后,进料盘中剩余的物料。
生产后生产的粉剂应及时装入干净的容器中,并注明产品名称、规格、批号、重量(数量)、生产日期、操作人员和审核人员等,送中间站保存备案,并提交车间技术员。
车间技术人员根据生产安排,将合格粉料放入下一批同规格品种的产品中,并要求在批次生产记录中注明粉料的物料流向。粉头必须有规定的使用期限,超过规定期限后必须重新检验,合格后方可继续使用。不合格的粉末应作为废物处理。
② 生产过程中产生的废弃物管理
生产废弃物是指在生产过程中不合格的物料和其他不能连续使用的物品,包括掉在地上的物料,以及压片或压片过程中填充量不同(片重不同)后的片剂。胶囊填充。(胶囊)、盛装物料的塑料袋等。应按照废弃物管理规定,生产经营者应及时将废弃物放入盛放废弃物的专用容器中,并在规定的时间由相关人员收集。专人通过物料通道离开洁净区。
下例生产过程中产生的物料如何处理?
粉碎后操作后留在粉碎机内的药物;
造粒过程中颗粒不慎掉在地上;
取出颗粒,观察干燥过程中颗粒的外观;
压片前压力测试(调整)后剩下的片剂;
对普通片剂进行取样和检查片剂重量的差异;
胶囊充填过程中,怀疑存在充填量差异不合格的胶囊;
造粒后发现丝网破损后有颗粒存在。
12.物料平衡管理
建立并规定物料平衡检验标准,严格控制生产过程中物料良率的变化,进行严格的良率控制,使其在合理范围内,对异常情况进行分析和处理,这是防止失误和混乱的重要手段之一。有效的方法。
①物料平衡计算公式
实际值收益率 = ×100% 理论值 其中:
理论值:是根据所用原材料(包装材料)计算的理论产量(生产过程中没有任何损失或错误的情况下获得的最大数量)。
实际值:是生产过程中的实际产量。
如造粒过程的物料平衡计算公式
所得颗粒总重量(kg) 物料平衡=×100% 投入原料和辅料重量+粉头重量(kg) 一般口服固体制剂物料平衡计算程序研讨会如下:
准备(粉碎,筛分);制粒和药物;起球、压片、胶囊填充;涂层; 内包装;外包装。
中药前处理工艺:药材选择;加工; 提取和浓缩;药材的干燥。
②生产过程中如有跑料,应及时通知车间管理人员和质量管理部门,并详细记录跑料的过程和数量。运行物料量也应计入物料平衡表,并加到实际值范围内。里面。
物料平衡良率不符合生产工艺规程要求的,应立即加贴待处理产品的状态标志,不得移交下道工序。
清关管理
一、定义和目的
为防止出现混淆和错误事故,在生产结束前和品种、规格或批号变更前,应将各生产工序清零。
场地清理频率:每天生产结束后清理,清理设备表面和操作室;更换品种、批号时,应彻底清理场地;连续生产规定时间(一般为三天)后,还应彻底清理场地;经过较长的生产间隔后,在重新开始生产之前也应清理场地。
场地清理必须严格按照岗位和设备的清洁程序进行。质量管理部门的车间工艺技术员、质量员和质量监督员对现场清理工作进行监督。
二、清关内容及要求
1.地面无积尘,无结垢,门窗、室内照明、风管、墙壁、开关盒等外壳无积尘。与下次生产无关的物品(包括材料、文件、记录等)不得存放在房间内。和个人杂物);
2.使用的工具和容器应清洁,无异物和油脂;
3.设备内外无生产残留药品不合格品控制程序英文,无油脂;
4.非专业设备、管道、容器、工具应按规定进行拆卸、清洗或消毒;
5.所有与药物直接接触的设备、管道、工具、容器等应每日或分批清洗或清洗。当同一设备连续生产同一无菌产品时,可按生产工艺规程和标准操作规程执行基本清洗周期;
6.包装流程清理完毕后,所有多余标签、说明书等包装材料均按规定处理。
三、清关记录和证书
场地清理时应填写场地清理记录。记录应包括工序名称、上批产品名称、规格、批号、清场日期、清场项目及检验情况,以及清场员和检验员的签字。
现场清关结束,车间质量人员审核通过后,出具清关证明原件和复印件。正本计入本批次生产记录,副本流入下一批生产记录。无上批清关证明复印件,车间不得进行下一批产品的生产。
【药品生产管理流程】相关文章:
1.药品生产管理流程
2.生产管理流程计划
3.生产管理的主要流程
4.药品生产管理中的风险管理分析
5.服装生产管理流程及规范
6.工厂生产管理流程及制度
7.如何优化生产管理流程
8.生产管理流程标准化的特点
请登录后发表评论
注册
社交帐号登录